SIL Inline Single Stage Centrifugal Pumps
Applications
The SIL pump range has been designed to meet the process requirements in versatile general and industrial applications to pump.
- Clean and slightly contaminated liquids
- Viscous liquids up to 250 cSt
- Fibrous slurries up to 1% consistency
Areas of application:
- Oil and gas
- Hydrocarbon processing
- Power generation
- Pulp and paper
- General industry
- Chemical process
- Industry
- Water and wastewater
Key Customer Benefits
The SIL pump range has been designed using our long experience and in-depth knowledge of how to maximize value for our customers. Key benefits include:
Premium efficiency
- The inline pump exceeds the EU’s (European Union) requirements for energy-relatedproducts (ErP)
- The whole pump range exceeds MEI 0.4 (Minimum Efficiency Index)
First class reliability
- The pump construction is optimized for clean liquid applications to maximize the lifetimeof the pump
- Monoblock construction means compact, rigid and reliable design eliminating the needfor a bearing unit. This minimizes the wearing parts and need for maintenance.
- Optimized shaft seal chamber and balancing holes guarantee improved conditions forthe shaft seal maximizing its life time
Minimized total cost of ownership (TCO)
- Low energy consumption due to high efficiency
- Low operational costs, low spare parts costs and minimized service due to trouble-freemonoblock construction
- Low installation and maintenance costs due to easy installation and simple design
Operating data
|
50 Hz
|
60 Hz
|
Capacities |
up to 720 m3/h |
up to 3,200 USgpm |
Heads |
up to 100 m |
up to 328 ft |
Pressures |
up to 16 bar |
up to 230 psi |
Temperatures |
up to 180°C |
up to 356°F |
Maximum speed of rotation |
up to 3,600 rpm |
up to 3,600 rpm |
Shaft seals
Large variety of mechanical shaft seals for maximizing operational reliability and minimizing downtime costs. The shaft seal is selected according to the application to ensure reliable shaft sealing. A large bore seal chamber guarantees optimal conditions and good lubrication for the seal faces. There is a large variety of shaft seals to fulfill the needs of various pumping conditions.
Single mechanical seal
- Positive inlet pressure is required
- The seal faces are lubricated by the pumped liquid flowing throughthe impeller balancing holes into the seal chamber
- Suitable for clean and slightly contaminated liquids
- Temperature 10°C / 20°F below the boiling point of the pumpedliquid at atmospheric pressure, max. 120°C / 250°F
Single mechanical seal with recirculation flushing
- The seal faces are lubricated by the pumped liquid circulated througha pipe from the discharge pipe into the seal chamber
- Suitable for clean liquids, water and condensates
- Temperatures up to 150°C / 300°F
Single mechanical seal with external clean flushing
- The seal faces are lubricated by external clean flushing liquid fedthrough a pipe from an external source into the seal chamber
- Suitable for clean and slightly contaminated liquids as well as viscousliquids
- External flushing is mixed into the pumped liquid
- Temperatures up to 180°C / 356°F
Double mechanical seal with external sealing liquid
- The seal faces are lubricated by non-pressurized (quench) orpressurized (barrier) external clean sealing liquid fed through a pipefrom an external source into the seal between the seal face pairs
- Designed for clean and slightly contaminated liquids as well asviscous liquids
- Temperatures up to 180°C / 356°F
Impeller
The efficiency, stability and reliability of the pump are based on the design. The impeller is designed in tandem with the casing and seal chamber. The result is efficient hydraulics with reliable shaft sealing ensuring higher reliability. The closed impeller is designed to suit versatile liquids maximizing standardization and minimizing the need for spare parts.
Design
- Closed impeller for clean and slightly contaminated liquids
- High efficiency
- Low net positive suction head required (NPSHr)
- Sturdy and strong design
- Optimized balancing holes
Impeller balancing holes guarantee optimized flow and pressure in the shaft sealing area
- Dry running of the single mechanical seal is eliminatedacross a wide operating area
- Increased reliability and lower downtime andmaintenance costs
Keyway impeller mounting
- Easy and quick dismantling and assembly
- Allows reverse rotation
- Minimizes downtime and maintenance costs
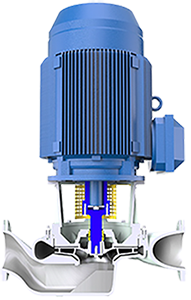
Drive motor
SIL pumps are of a monoblock construction. They are equipped either with an integrated AC motor or with an IEC standard motor.
Integrated motor construction
- The motor is integrated into the pump
- The impeller is installed directly onto the motor shaft withoutany coupling
- Available efficiency grades IE3
- Available power range 0.05 - 160 kW
- Available in 2-pole and 4-pole models
- The motor is VFD compatible
- The pump and motor combination is very compact and quickto install
- Pumps equipped with a max. 15 kW motor can be installedbetween the pipes without additional support or base plate
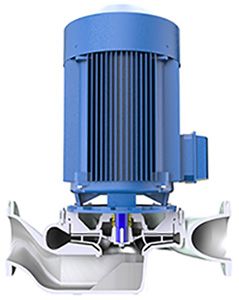
IEC standard motor construction
- The motor is an IEC standard low voltage flange mountedAC-motor
- The motor is installed to the pump with an adapter
- The impeller is installed to a flange shaft which is connectedto the motor shaft with a coupling
- Available efficiency grades IE2, IE3, IE4
- Available power range 4 - 110 kW
- Available in 2-pole and 4-pole models
- The motor is VFD compatible
- The pump and motor combination is compact and quickto install
Performance ranges
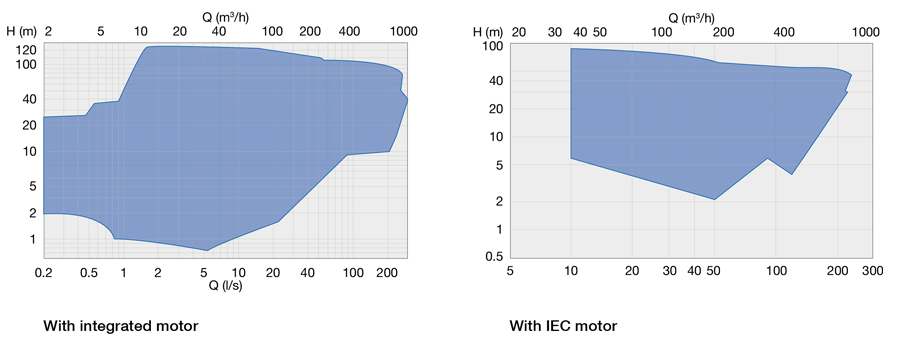
Materials
Standard material options
|
|
|
|
Cast Iron |
ASTM |
A48 CL30 |
ENGJL200 |
Ductile Iron |
ASTM |
A536 |
ENGJS400 |
Austenitic
|
ASTM |
A743 |
Grade CF-8M |
Austenitic
|
ASTM |
S31254 |
SS2378 254 SMO |
Duplex SS |
ASTM |
A890 |
Grade 3A |
Bronze |
ASTM
|
B505
|
CuSn10Zn2
|