THE WORLD'S FIRST SUBMERSIBLE MIXER CONCEPT WITH A PERMANENT-MAGNET MOTOR.
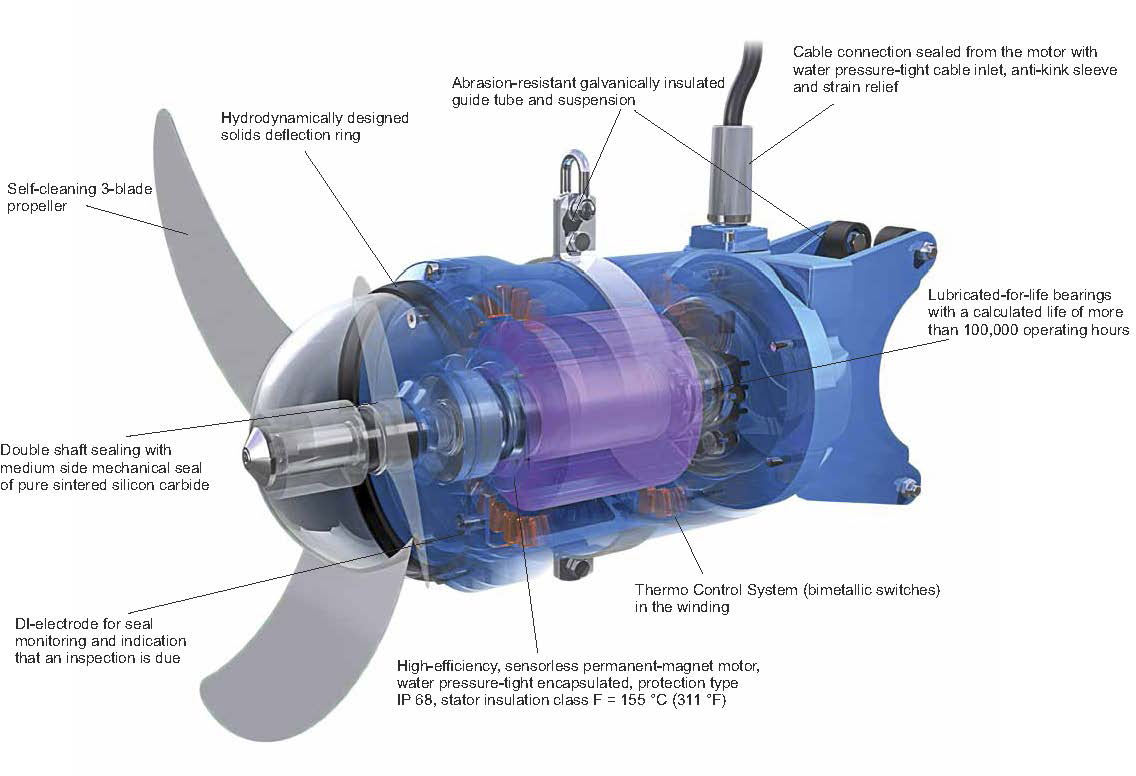
A mixer called the Sulzer submersible mixer XRW was first introduced in 2010 as a medium-speed mixer concept with a permanent-magnet motor. Now it has been expanded into a full product range, covering high, medium and medium-low mixing speeds. To retain the mixer’s unique blend of energy efficiency and economy, three motor technologies have been used. Medium-speed versions retain the permanent-magnet motor, while the others utilize an IE3 squirrel-cage motor, supported by a gearbox at medium-low speeds. Using the most appropriate motor technology produces the best balance of equipment price, motor efficiency and long-term operating costs.
The Sulzer submersible mixer concept XRW for wastewater treatment not only offers you long-term reliability, minimal maintenance and maximal equipment life-cycles for optimal life-cycle economy, but also greater energy saving to cut power consumption and reduce the CO2 footprint.
The major benefits:
- Lowest energy consumption. Using IE3 permanent-magnet motors together with optimized and proven propeller designs enables the Sulzer submersible mixer concept XRW to achieve the lowest energy consumption possible for medium-speed mixing. You gain a total efficiency improvement of up to 35% compared with other existing medium-speed mixer designs.
- Greater process control. Variable-speed drive that allows processes to be optimized and energy consumption to be minimized in addition to the energy savings obtained through using high-efficiency equipment designs.
- Fewer mixers for wide application. Our new technology using variable-speed, permanent-magnet motors results in a limited number of basic mixer sizes that still covers a wide range of applications. This greatly reduces the need to stock spare equipment and parts without increasing the risk of operational downtime.
- Cost-effective maintenance. The combination of compact design and considerably reduced weight allows easy mixer installation and removal. Together with fewer basic mixer sizes and the EffeX Exchange Program for permanent-magnet motors, you get cost-effective maintenance without the need for specialist equipment.
- Superior reliability. Much greater reliability of the new submersible mixer concept XRW results from:
- High overload capacity
- 100,000-hour bearing life with a better bearing environment achieved by using low-temperature IE3 permanent-magnet motors
- Optimized mechanical seal
- Enhanced solid deflection ring design
No brushes, VFD-driven
Other crucial factors in driving the development of permanent- magnet motors – also known as brushless AC synchronos electric motors – are the high cost of copper, which has less impact on permanent-magnet motors because they lack rotor windings, and cheap electronic components, especially power transistor equipped variable frequency drives (VFD). Instead of slip ring, brushes and windings, permanent magnets are mounted on the rotor. This overcomes the problem of how to transfer current to a moving armature. A VFD is used in conjunction with high-power transistors to charge up the electromagnets as the rotor turns.
Controllers direct rotation
With permanent-magnet motors, a controller involving an algorithm is used to direct the rotation of the rotor. To enable this, some designs use Hall effect sensors or a rotary encoder to directly measure rotor position. Others measure the back electromotive force (EMF) in the windings of the stator magnets to determine rotor position. As this avoids using Hall sensors, this type of design is often called sensorless controllers. This type of motor control is used in the submersible mixer concept XRW.
And although these motors have a higher initial cost, this is quickly recovered through their greater efficiency significantly reducing energy consumption.
The many benefits of permanent-magnet motors include:
- Higher motor efficiency within a wide speed range;
- Greater reliability and longer lifetime;
- Lower operating temperature;
- Compact design and less weight;
- Lower electrical power to drive the motor;
- Flexible system operation.
As there are numerous applications that demand one or more of these benefits, the future looks bright for permanent-magnet motors.
Highly Effective Mixing In WWT Plants
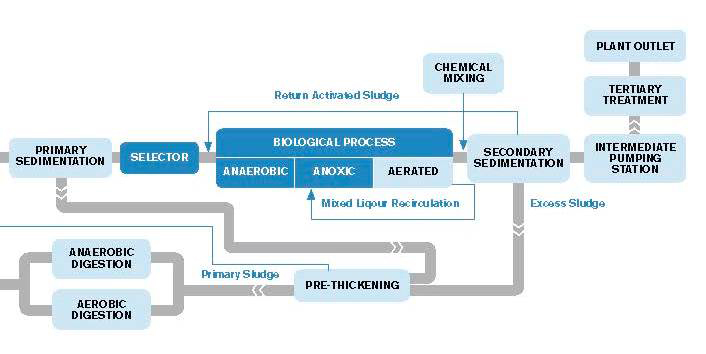